Outdoor fiber optic cables transport data and communications signals over long distances while enduring extreme environments. As the backbone of modern telecom infrastructure, these cables come in specialized designs to operate reliably despite the challenges of humidity, tension, wind, rodents, and other outdoor threats. This article summarizes the major outdoor cable varieties and their distinguishing features.
Table of Contents
Loose Tube Cable
Loose tube cables encase the delicate glass fibers in protective buffer tubes filled with gel. This prevalent outdoor cable type balances flexibility and robustness.
As per industry standards like IEC 60794-3-10, loose tube cables arrest external moisture ingress thanks to the water-blocking gel surrounding the optical fibers. The loose buffer tubes also shield the fibers from physical damage while allowing adequate movement to maintain signal stability over a wide temperature range of -40°C to +70°C.
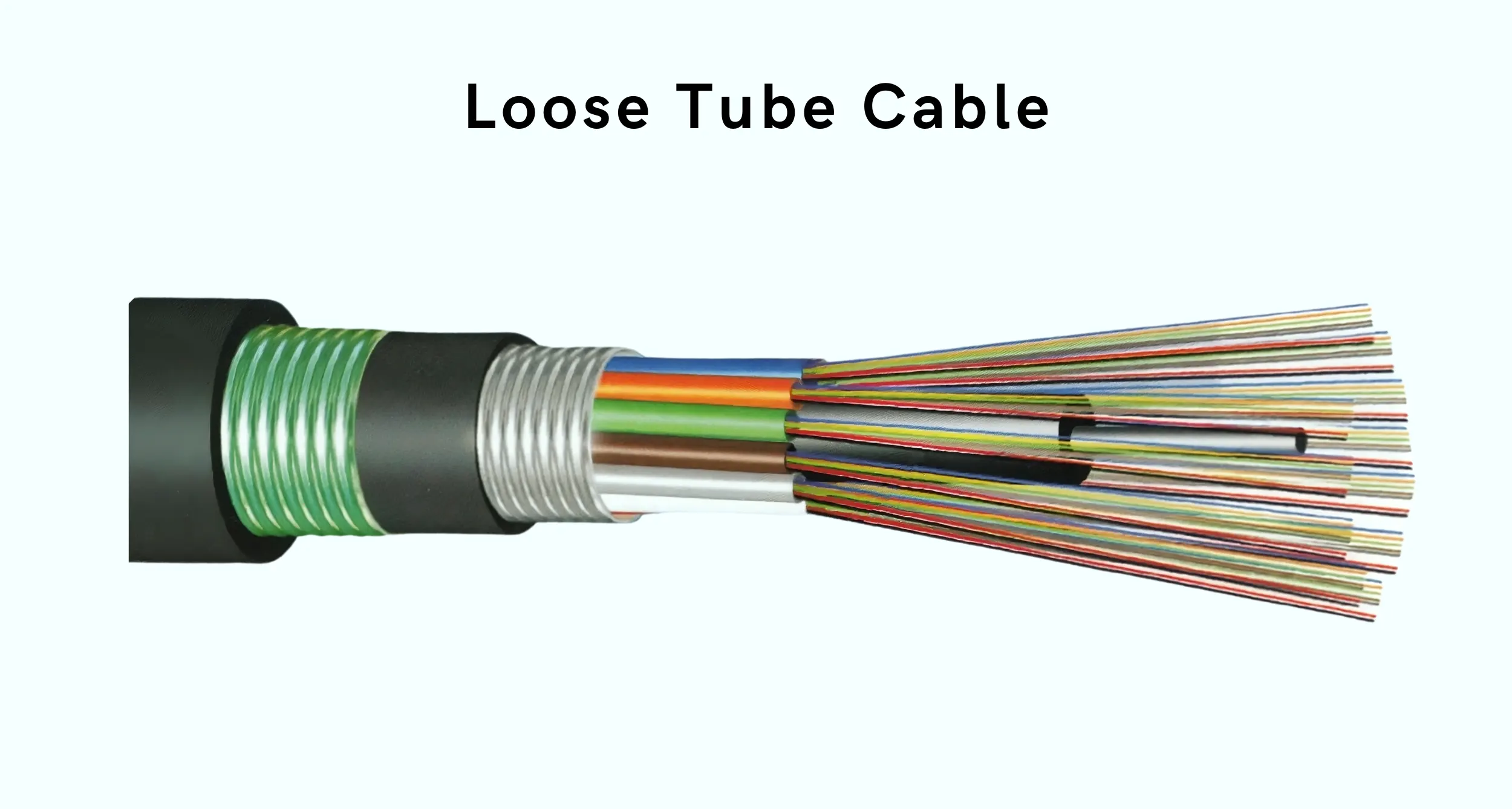
The gel-filled buffer tubes and moisture-resistant construction equip loose tube cables to thrive in high humidity outside plant environments. Their rugged yet flexible design makes these cables suitable for exposed conduit runs and the transition between outdoor and indoor network segments.
With crush-resistant exteriors shielding the fibers from harm, loose tube cables deliver dependable performance despite the knocks, scrapes, and moisture exposure endemic to outdoor installation sites.
Key features:
- Protective gel surrounds fibers, blocking moisture ingress
- Loose tubes allow stable transmission despite temperature changes
- Ideal for high-humidity conditions and outdoor-to-indoor transitions
Loose tube cables balance protection and flexibility to deliver reliable performance where exposed to rain, dirt, extremes of hot and cold, etc.
Micro Cable
Micro cables cram multiple optical fibers in miniaturized cross-sections, reaching diameters between 1-2mm versus 10-15mm for regular cables. These ultra-compact cables allow dense fiber deployment thanks to high fiber packing density – with easy maneuvering through congested conduits.
The small size yields big advantages. Micro cables are 50% smaller in diameter and 70% lighter in weight compared to traditional loose tube cables. This svelte profile cuts down duct occupation and simplifies installations. Their versatility makes micro cables suitable for long-haul networks and connecting nearby buildings.

Developed to meet surging connectivity demands, micro cables are now ubiquitous in local area networks, fiber-to-the-home (FTTH), or office (FTTO) rollouts. Their space and weight savings translate directly into lower costs – both operational and capital expenditure.
Be it within congested building risers or laid over kilometers, micro cables maximize fiber density without compromising ruggedness. Their diminutive footprint drives modern high-capacity network buildout.
Salient specifications:
- 50% smaller and 70% lighter than standard loose tube cables
- Diameters as tiny as 1-2mm
- High fiber counts in limited space
- Common in LANs and buildings where space is limited
Their extremely small footprint makes installing micro cables easy, even in congested conduits and pathways.
Ribbon Cable
Ribbon cables squeeze multiple optical fibers side-by-side in a common outer jacket for efficient space utilization. The fibers are bonded as a cohesive ribbon, typically with up to 12 fibers per ribbon.
Originally designed for outdoor installations, ribbon cables now find widespread use in premises cabling as well, given their ability to maximize fiber density. The low-profile flat ribbon structure packs more strands per square inch versus loose tube or round cables.
Compared to loose tube cables, ribbon cables also offer lower latency thanks to the shorter distance between fibers. This compact arrangement also streamlines cable management during installation and maintenance.
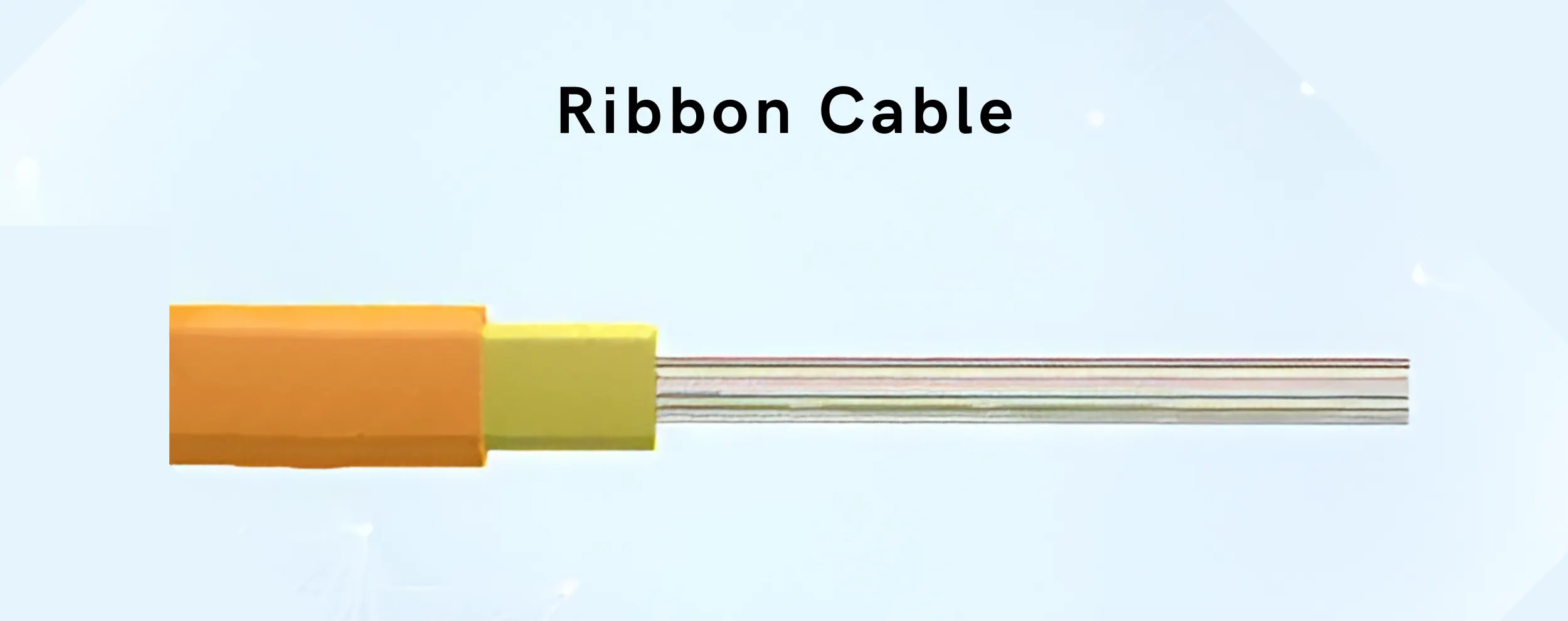
Modern ribbon cables employ advanced materials like fiber-reinforced plastic as a protective layer. This enduring sheath shields the internal glass fibers from mechanical damage as well as moisture despite the limited overall diameter.
With major manufacturers offering specialized variants for harsh long-haul outdoor as well as plenum or riser ratings for in-building use, ribbon cables deliver top-tier capacity and safety across application scenarios.
Major merits:
- Enables high-density fiber packing
- Compatible with multi-fiber connectors
- Low cable diameter with up to 12 fibers
- Simplifies cable management
While originally designed for outdoor spaces, ribbon cables are now ubiquitous in premises networks for their space efficiency.
Armored Cable
Armored cables employ an extra metal jacket layer to protect the optical fiber core against aggressive environmental factors, including rodents, abrasion, impacts, and twists.
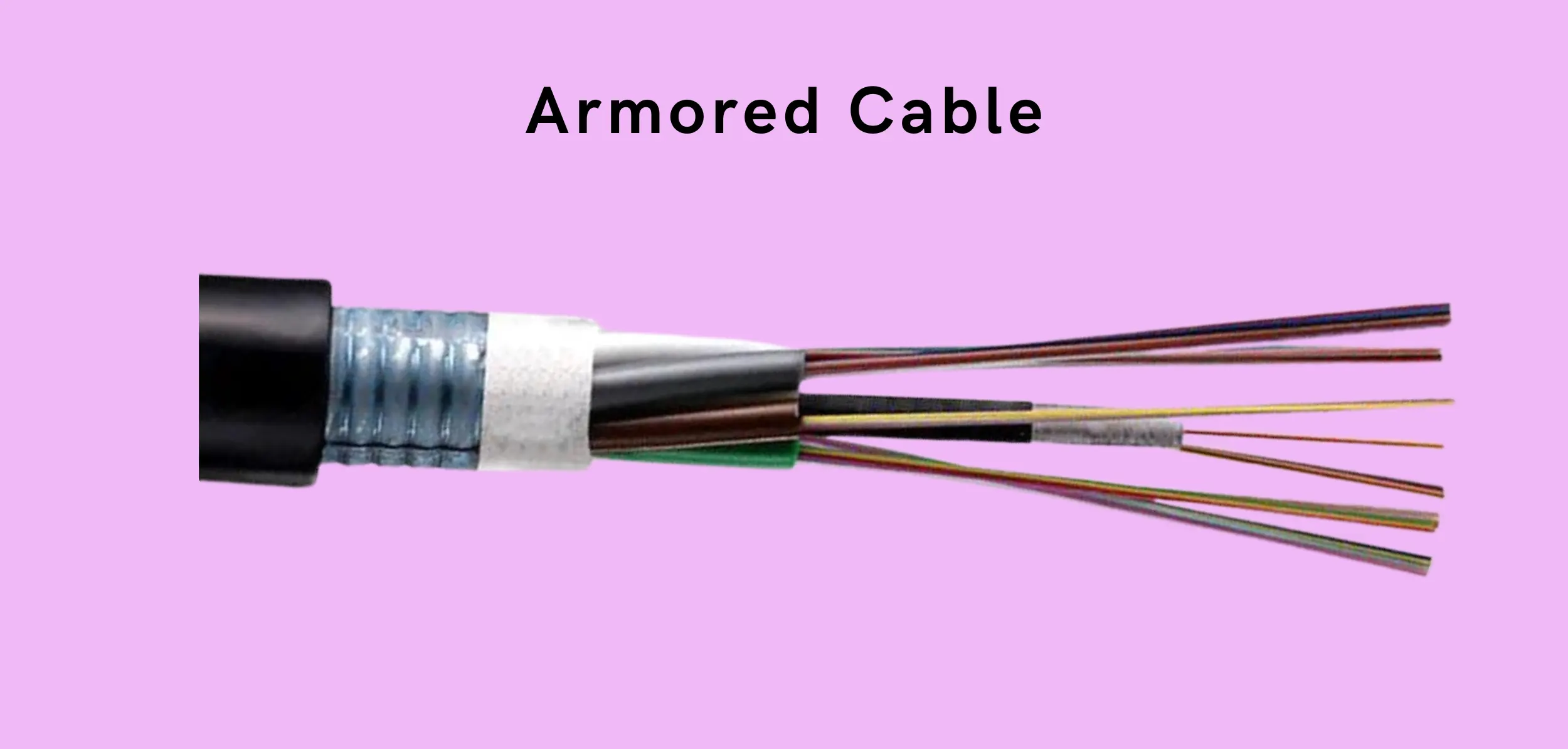
Popular armoring types include:
- Interlocking armor: A helical aluminum metal sheath provides all-around mechanical protection. This bellows-like interlocked metal exoskeleton absorbs crushing impacts, making it suitable for installations subject to weight or severe compressive loads.
- Corrugated armor: Longitudinal corrugated steel tape shielding the cable from rodent attacks. The fluted steel encasing deters bites and chewing damage.
The metallic reinforcement boosts installation costs but also enhances reliability in vulnerable outdoor routes facing heightened vandalism or critter risks. Proper armored cable selection balances cost, risk, and performance targets.
Figure-8 Cable
Figure-8 aerial cables employ a namesake design with curving vertical lobes to prevent the accumulation of ice or debris on top. The shape balances rival needs – lightness for easy suspension while still granting strength to counter wind pressure and ice loads.
Crafted as per standards like ITU-T L.102, these self-supporting cables require no separate messenger wire. Instead, the integrated dielectric strength member bears the cable’s weight across spans extending to several hundred meters.
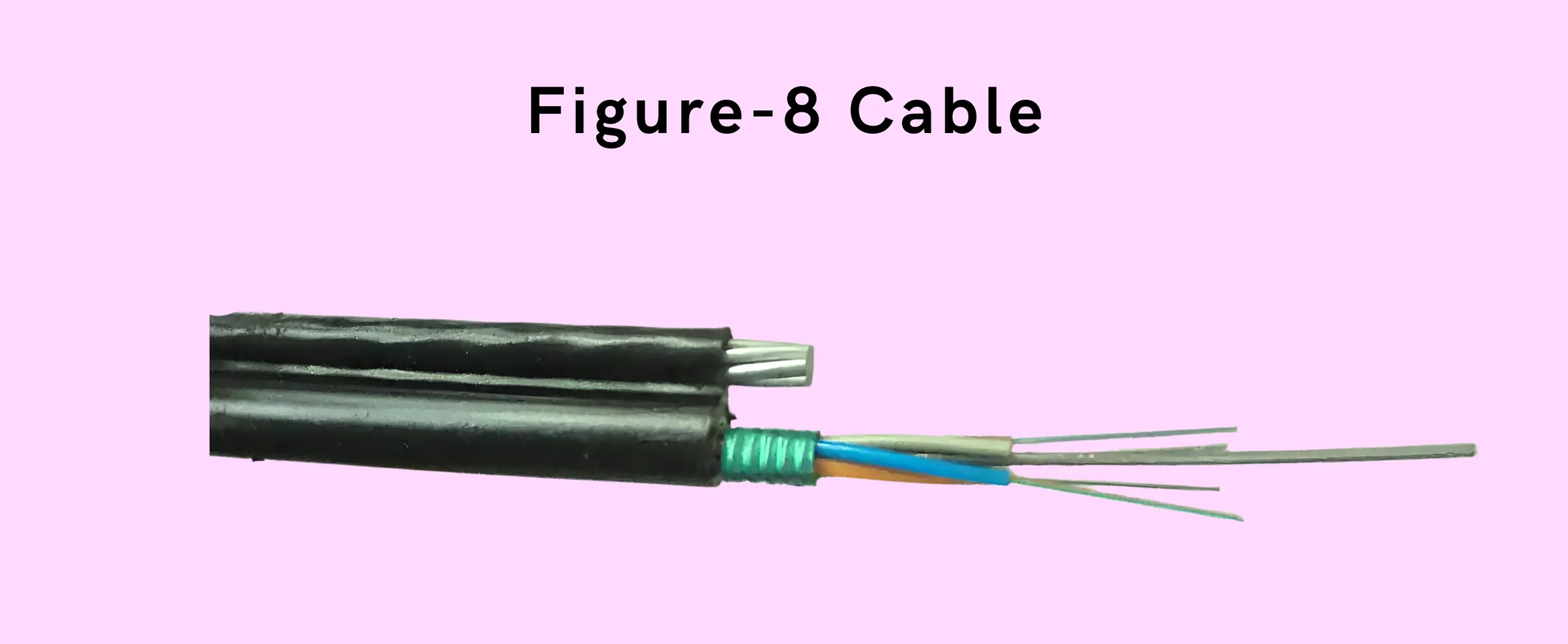
Figure-8 cables also shrug off outdoor stressors, including ultraviolet radiation, twisting forces, and temperature swings from -40°C to +70°C. The rugged construction protects the typically jelly-filled buffer tubes housing up to 12 fibers apiece. Careful stranding allows handling down to -30 °C installation temperatures.
With options for rodent-resistant armor and more, figure-8 cables reliably convey large communications bandwidth aerially between poles. Their balance of strength members, conductors, and fibers suits most overhead line applications.
Key qualities:
- Messenger wires independently support the cable
- Waterproof & weather-resistant construction
- Capable of supporting extra anti-rodent sheathing
Their sturdy build makes figure-8 cables well-suited for lines strung between utility poles.
Duct Cable
Duct cables robustly shield optical fibers across buried conduit spans. Network builders either pull factory-terminated duct cable lengths through conduits or blow bare fibers sticking out of conduit ends, subsequently getting spliced.
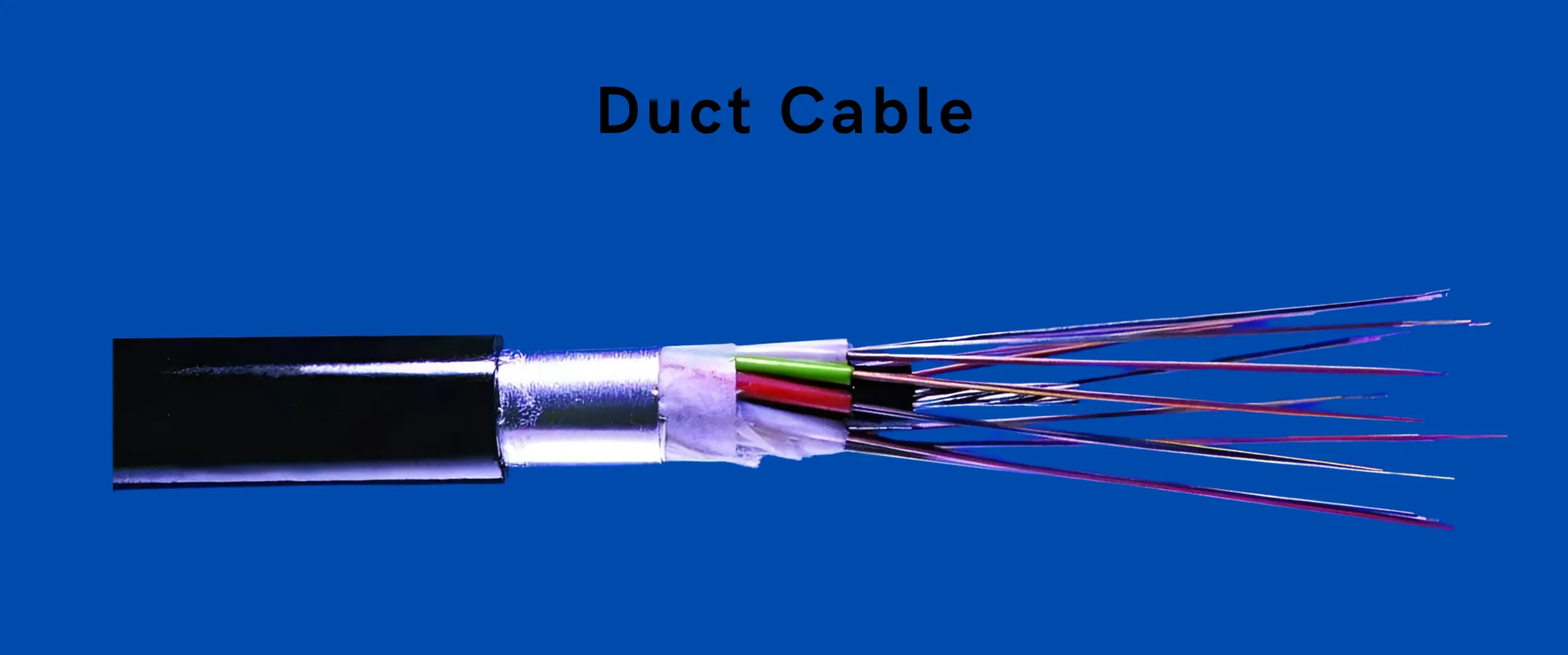
Per standards like ITU-T L.100, duct cables are custom-built to withstand the tension of pulling sizable lengths at speed through ducts while resisting water and chemicals. Common specifications include:
- High tensile strength – for pulling/blowing longer segments
- Durable abrasion-resistant polyethylene jacketing
- Water-blocking tapes limiting moisture propagation
Proper duct cable sizing, materials, and pulling calculations prevent undue stress during installation. Once hauled into position, duct cables deliver reliable performance for decades encased safely underground.
Drop Cable
Drop cables connect the main distribution cable traversing a region to end-user homes or commercial buildings. These cables bridge the final stretch from the fiber backbone to the premises – often called fiber to the home (FTTH).
As per ITU-T L.105, drop cables have:
- Low fiber count – typically 2 to 12 strands
- Limited diameter – generally under 15mm
- Maximum length of around 80 meters between poles
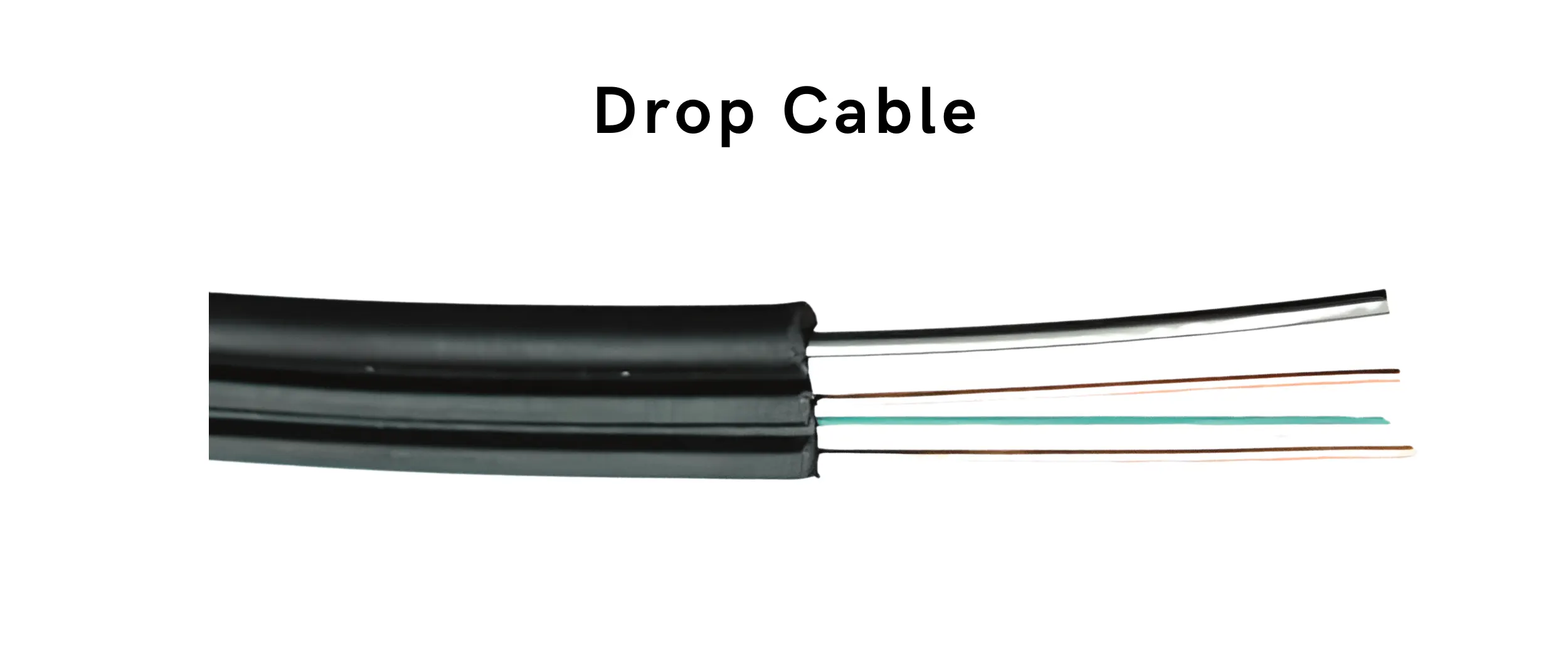
Common drop cable types include:
- Flat dropout – Ribbon fibers sandwiched by glass fiber strength members
- Figure-8 – Suspended aerially using integrated messenger wire
- Round – Circular cross-section for conduit/direct burial
While weatherproof jacketing protects the fibers, installer diligence is vital when drilling conduit holes or securing overhead lines. Rodent guards and armoring are worthwhile investments for drop cables facing elevated exposure risks before disappearing into the premises.
Hybrid Cable
Hybrid cables integrate both optical fiber and copper elements within a shared outer sheath. This economical bundling serves many purposes:
- Copper components enable direct power feeding to remote cable ends
- Optical fibers carry high-speed data with immunity against electromagnetic interference
- Eliminates the need for separate cable infrastructures, lowering costs
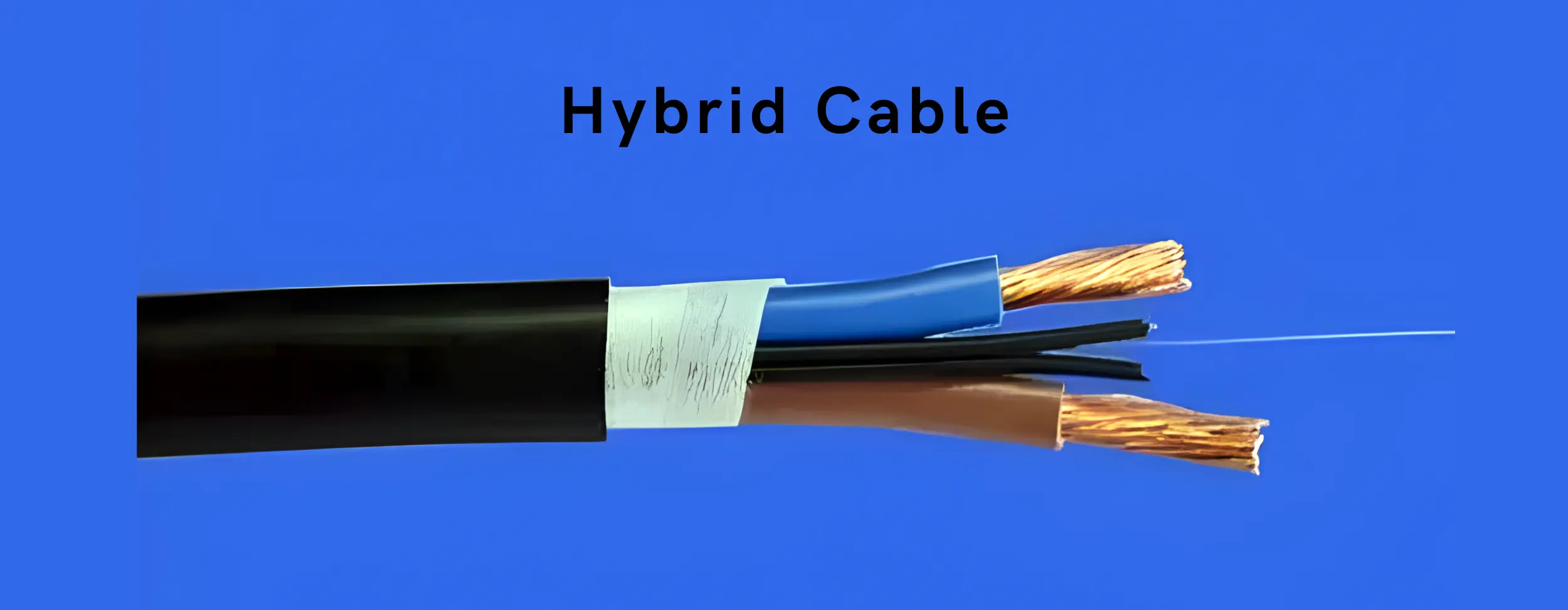
A hybrid cable’s fiber count and copper gauge fit application requirements spanning copper’s shorter networking reach yet higher raw power capacity.
Uses include:
- FTTx/5G small cell deployment
- Connecting wireless access points
- Temporary outdoor networks for events
- Smart lighting/sensing, traffic signals
Network architects harmonize optical and electrical conduits with hybrid cables in one unified system. This potent fusion transmits data at light speed while energizing equipment over the same lifeline.
All-Dielectric Self-Supporting (ADSS) Cable
All-dielectric self-supporting (ADSS) cables employ internally reinforced plastic jacketing rather than metal wires to string overhead fiber lines securely between poles.
As ADSS cables have no conductive metal components, they avoid interference when mounted near power equipment. The dielectric design also saves the cost of grounding wires while easing logistics.
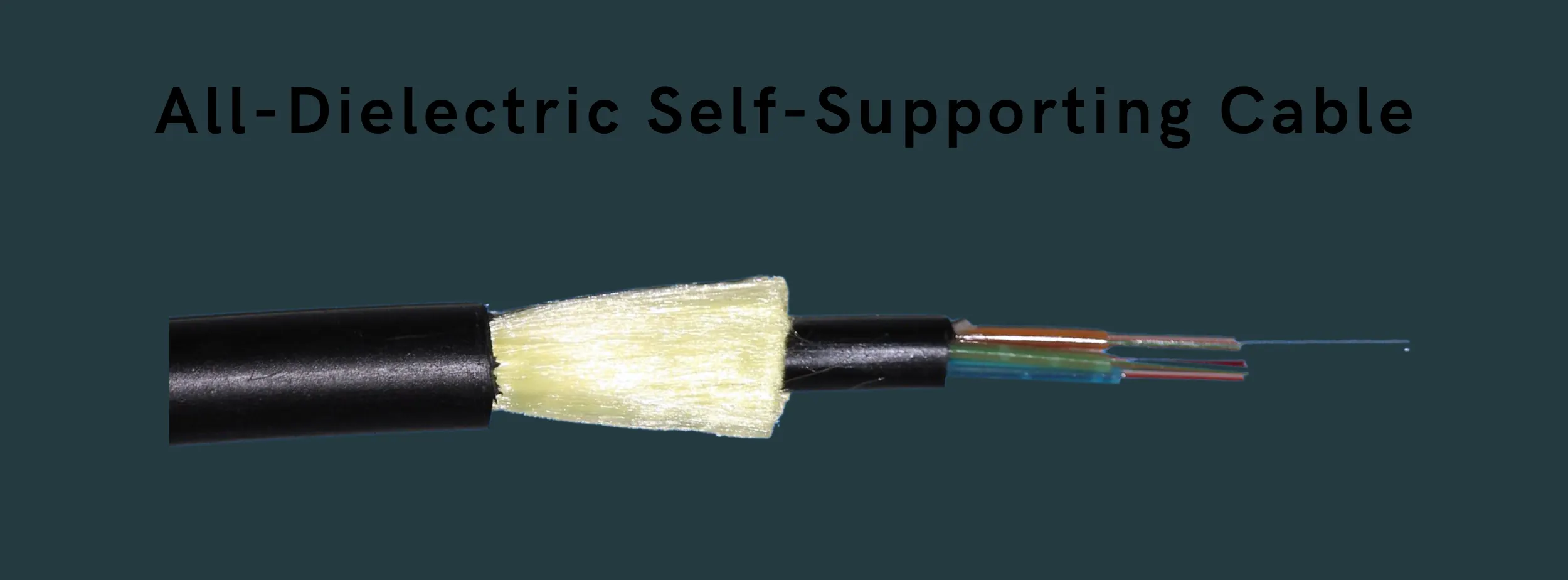
ADSS cable structure per IEC 60794-4-20:
- Central loose tube/ribbon cable with up to 288 fibers
- Reinforcing glass/ceramic rod and Kevlar/fiberglass strength members
- UV-resistant polyethylene outer sheath
This lightweight yet strong assembly spans up to 5000 feet unsupported despite winds, ice, and temperatures from -40°C to +70°C. The versatility makes ADSS cables ideal for both long-haul telco networks and campus layouts.
Optical Ground Wire (OPGW)
An optical ground wire (OPGW) clubs together fiber-optic data transmission with grounding/lightning protection for overhead high-voltage lines.
OPGW per ITU-T L151 integrates:
- Central loose-tube optical cable
- Outer layer of aluminum-clad steel wires
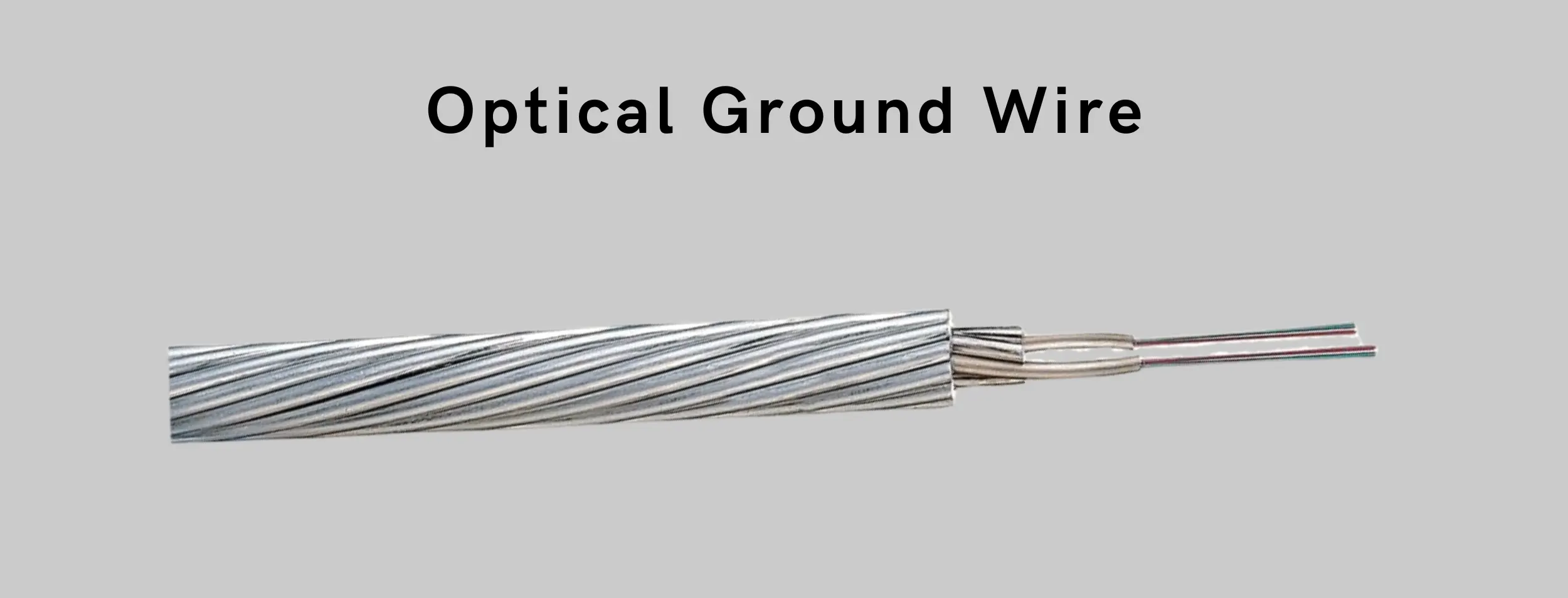
This hybrid functions as:
- Lightning arrestor as the primary grounding path
- Communication channel via embedded fiber
- Structural cable minimizing line infrastructure
With armor-resisting faults and metals to dissipate lightning strikes, OPGW cables enable smarter power grids with ~128 fibers for control signal exchange.
The consolidated design slims project complexity, cost, and real estate challenges associated with independent cable routes.
Submarine Cable
Submarine cables laid across ocean beds link continents through high-capacity optical fiber connectivity. These engineering marvels traverse thousands of kilometers underwater as critical conduits of global communication.
As per ITU-T G.654, submarine cables have:
- Fiber optic core with 10 to 100+ Tb/s capacity
- Layers of copper or fiber reinforcement
- Polyethylene/polyurethane protective covering
This robust build shields the invaluable fibers from crushing pressures, corroding saltwater, abrasive rocks, marine life, and fishing equipment.
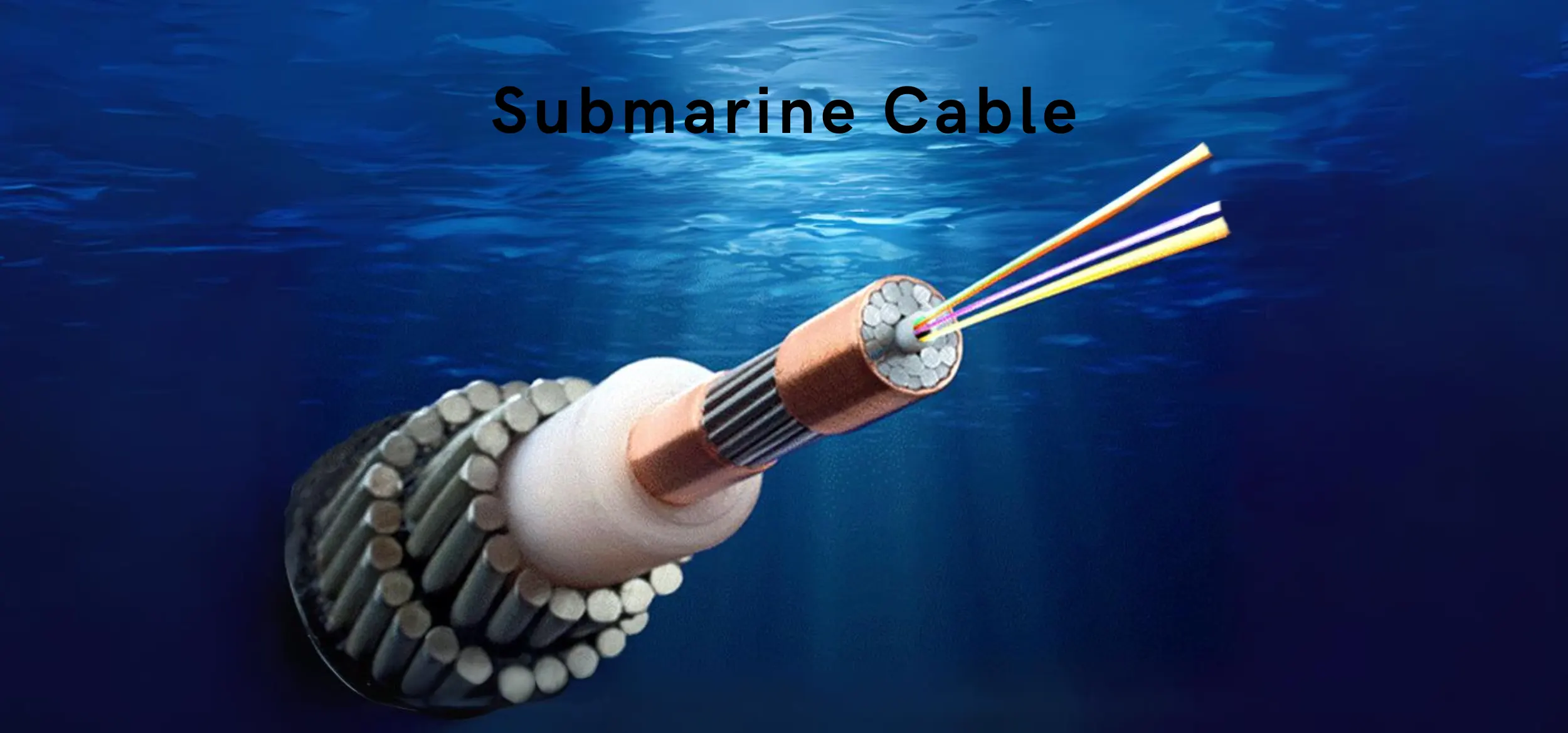
Repeater huts placed every ~50 miles amplify and resynchronize intermittent light signals across extended distances. Self-healing fiber rings bypass any localized damage for resilient performance.
Companies like TeleGeography map the 550+ active systems with interactive tools showing submarine cable landing points and technical attributes. These mesmerizing details underline the global connectivity made possible by frail submarine fibers traversing hostile seabed terrain.
Conclusion
The diverse outdoor optical fiber cables detailed in this guide – from micro ducts to transoceanic links – underscore fiber’s versatility. Cable designs match performance parameters with operating conditions across a vast range of locales and landscapes.
Whether winding through conduits barely wider than a finger or stretching between continents, optical fiber confers information mobility. The supporting cables engineered to overcome humidity, corrosion, storms, or geological pressures empower humanity’s global nervous system transmitting terabytes of data each second.
Careful outdoor cable selection unlocks fiber optics’ potential to deliver speed, density, and reliability – elevating networks to meet exponentially growing connectivity demands now and in the future across applications.
Here are the brief details of the outdoor fiber optic cable types that we discussed throughout the article.
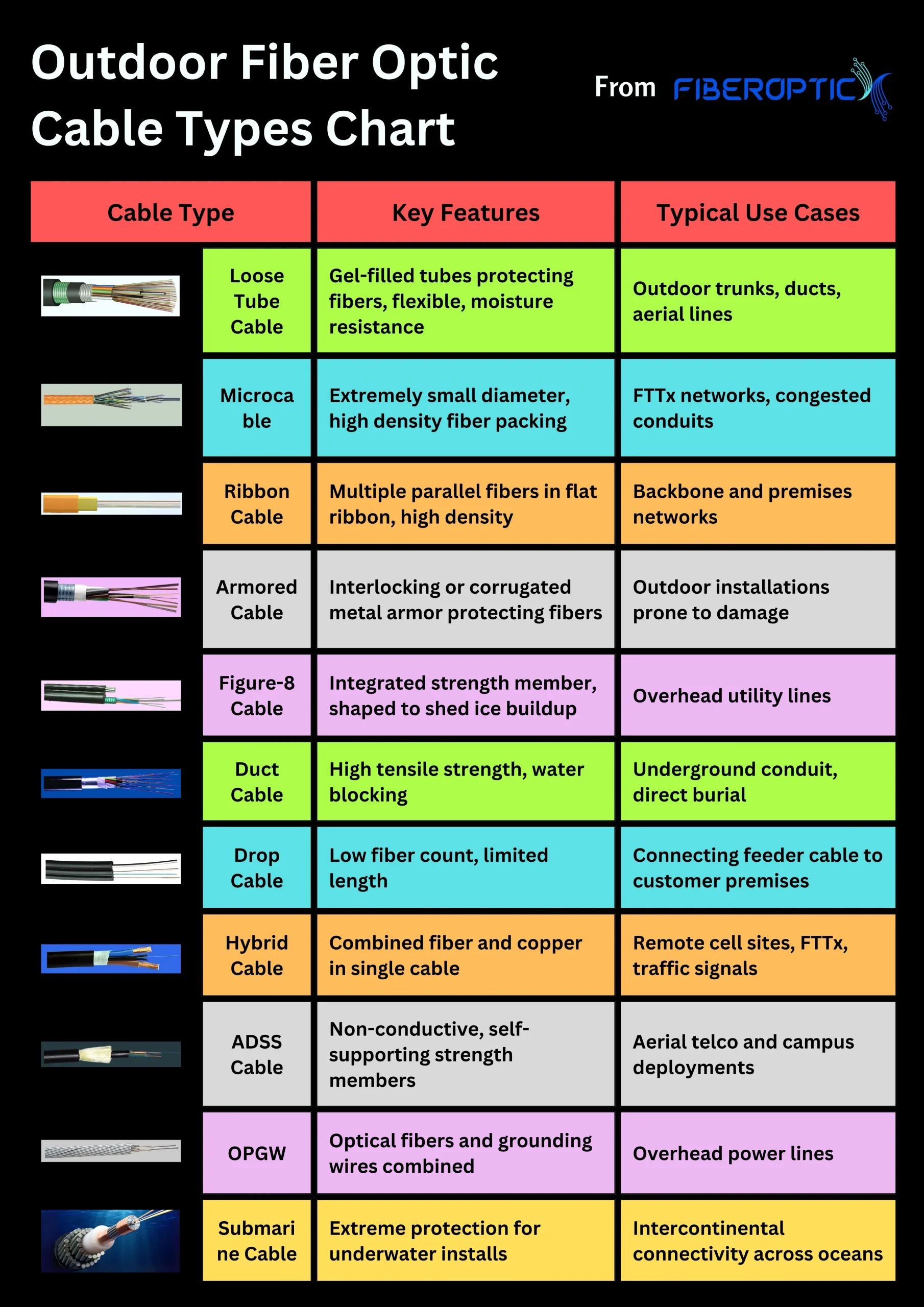
FAQ
Which cable type is mostly used for outdoor applications?
Loose tube cables are the most commonly used type for outdoor installations. They offer excellent protection for the fibers with their individual buffer tubes and gel filling, making them resilient to weather, temperature changes, and mechanical stress.
What are the 3 main types of cable installation for outdoor applications?
∎ Aerial: Cables suspended on overhead lines or poles, often using ADSS (all-dielectric self-supporting) cables for their strength and lightweight nature.
∎ Duct: Installed underground in protective conduits, typically polyethylene ducts, for additional environmental protection.
∎ Direct buried: Buried directly in the ground, requiring cables with robust features like armored construction and rodent-resistant materials.
What color are outdoor fiber optic cables?
Outdoor fiber optic cables usually come in black or dark grey, chosen for their ability to absorb heat and minimize the impact of sunlight exposure. This helps maintain cable integrity and performance over time.
What is the difference between indoor and outdoor fiber optic cable?
Outdoor cables require more robust construction for weatherproofing, mechanical strength, and rodent resistance. They often have thicker jackets, additional strength members, and gel filling for moisture protection. Indoor cables focus on flexibility and ease of termination with thinner jackets and simpler designs.
What damages fiber optic cable?
∎ Physical damage like crushing, cutting, or excessive bending.
∎ Exposure to extreme temperatures or prolonged sunlight.
∎ Moisture ingress due to improper sealing or cracks.
∎ Rodent or pest activity, if not protected.
∎ Improper cleaning or use of harsh chemicals.